Technology
Amiagus has developed comparable cheap thermal coating technology that solves very complicated task – getting good adhesion of the coating to metal strip substrate and at the same time obtaining needed porosity, surface and composition of it. Metal strip is coated by thermal spraying of metal oxides at the same time controlling and ensuring high and uniform quality of the coating through all width and length of the coated layer.
Fig.1. Spraying process
The main idea of our process is to spray powder materials that can be easily decomposed after spraying and to prevent these materials from decomposition in plasma stream as well as to get good adhesion to metal substrate. These requirements make the process very complicated and various methods are proposed for effective solution of this problem. Metal substrate of our catalytic coating is the key figure in the end product, because there are a lot of applications where usual ceramic support is not suitable or not economically effective.
Properties of the coated metal support:
- Good adhesion of the coating to the metal support. That allows to perform mechanical treatment - cutting, corrugation, twisting, rolling etc. after spraying without peeling of the sprayed layer (Fig.2);
- High thermal and electrical conductivity that gives an opportunity to change construction of the reactor to more efficient and heat catalytic block by electric current;
- Low weight compared to the most of ceramic substrates used for analogical purposes;
- High specific surface area of the coating compared to others metal based ceramic coatings - usually 70-80 m2/g but can reach up to hundreds of m2/g (Fig.3);
- Good resistance to mechanical and thermo shock;
- High thermal conductivity (22.9 W/(mºC) at 800ºC) due to metal strip support;
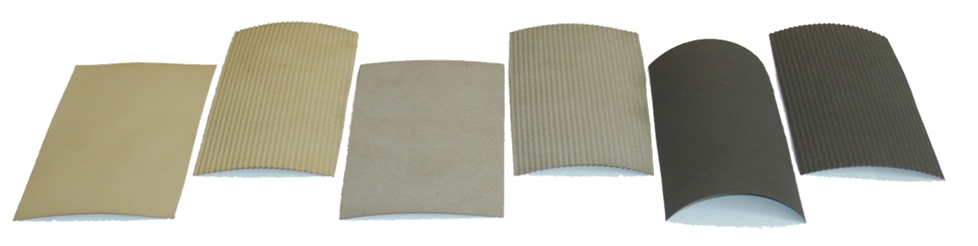
Fig.2. Flat and corrugated samples
Fig.3. Surface morphology of the coated layer
The base Amiagus thermal coating technology opens new ways for creating various catalytic coatings on different kinds of metal strips for wide range of applications:
- metal based catalysts for tar cracking
- metal based catalysts for hydrocarbon reforming
- rolled metal strip coated with catalytic support on one or both sides
Coated metal support is used to form metal based catalytic element with honeycomb structure. It is produced by rolling two both sides coated metal strips – one flat and one corrugated (refer to Fig.4), around a transversal axis.
Technological steps
Catalytic blocks are made in these technological steps:
- Deposition of coating by thermal spraying of ceramic based catalytic powders on both sides of metal strip (basically of 0.03-0.05 mm thickness and 45-100 mm width).
- One part of coated strip is being corrugated. One of the advantages of our technology – high adhesion of coated layer to the metal strip that allows us to perform corrugation without peeling of the coated layer.
- Formation of cylinder shaped catalytic block with honeycomb structure that consist of two rolled metal strips, flat and corrugated (Fig. 5 A-D). Block can be of any height (basically 45-100mm) and diameter of up to 200 mm and more.
Using our technology we are able to produce catalytic element with axial and/or radial gas transfer and longitudinal channels of triangular shape in cross-section. Catalytic element is shown on the Fig.5C. The diameter of the element depends on internal diameter of the tube, or other vessel used. The element in cross-section can be adjusted to oval or even rectangular shape.
Fig.5A-D. Honeycomb structure catalytic element
|
|
|
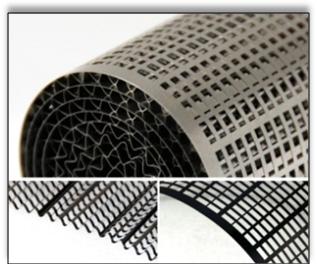 |
Fig.6. Block with axial gas transfer |
Fig.7. Block with axial and radial gas transfer |
- Effective properties of formed metal based catalytic block:
- Good adhesion of coated layer to metal substrate;
- Good resistance to thermal cycling and gas erosion;
- Low back pressure due to honeycomb structure and metal strip thickness;
- Low weight compared to most of ceramic pellets used for analogical purposes;
- About 10 times higher geometrical surface area of honeycomb catalytic unit compared to the same volume of ceramic pellets used for steam reforming process;
- High 22.9 W/(mºC) thermal conductivity at 800ºC due to metal strip support;
- Good metal support electrical conductivity that gives an opportunity to heat catalytic block by electric current;
Cooperation
Advanced thermal coating technology was developed during years of research (since 1995), laboratory tests, participation in European scientific projects and cooperation with partners: Fiat (Italy), Technical University of Viena (Austria), UNIBO - Università di Bologna (Italy), Technical Research Centre of Finland (VTT), POLITO (Italy), MEL Chemicals (UK), Gaz de France, C.S.I.C.- Universidad Politécnica de Valencia (Spain), GE JENBACHER and many others.
Using Amiagus technology we are developing and investigating catalytic units for tar cracking in gasification processes and catalytic units for hydrocarbon reforming processes. At the moment we have all technological equipment and we are able to produce catalytic block samples for laboratory and industrial like tests.